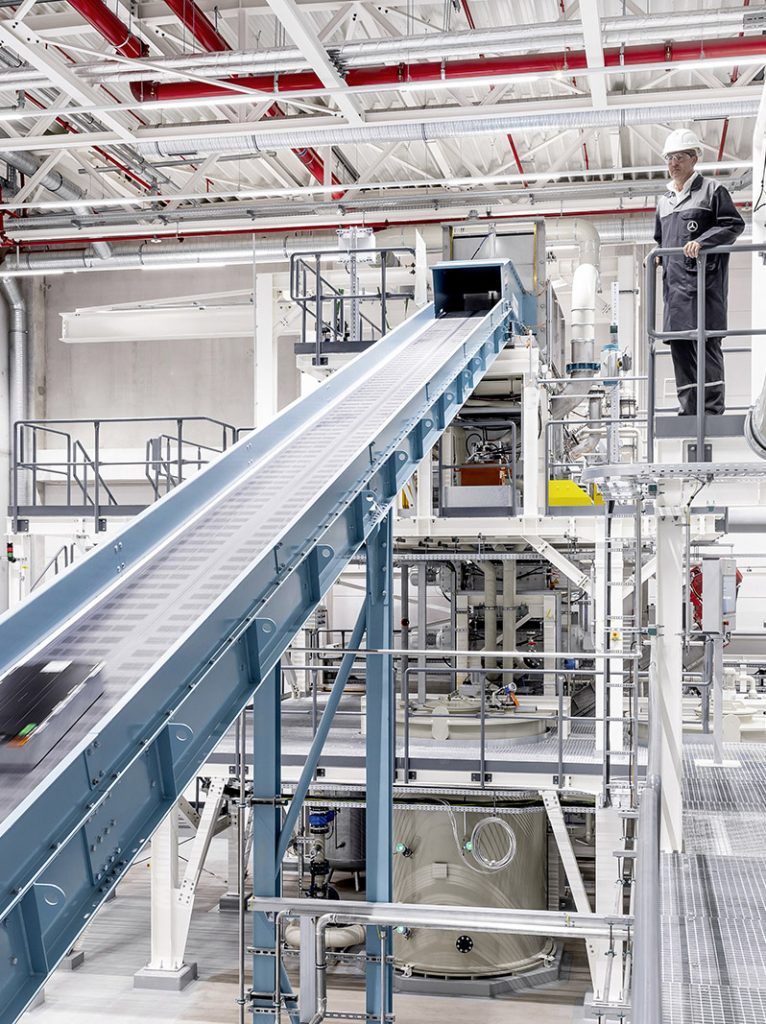
Mercedes-Benz opened a plant in Baden-Baden at the end of October to recycle batteries from which it hopes to recover more than 90% of their materials. The competition has only just begun.
The German giant claims that its new factory has an annual production capacity of 2,500 tons and that the recovered materials will feed the production of more than 50,000 battery modules for its new fully electric cars.
An analysis by S&P Global Mobility expects that by 2032, minerals recovered from used batteries will account for 21% of global demand for cobalt and 19% of the total demand for nickel. And European and American automotive giants have begun to react, even more so after their acquisition of batteries exploded last year until it ran into a supply crisis. And we’re not just talking about Mercedes-Benz here. Tesla is adding similar plants to that in Baden-Baden in its Gigafactories in Texas and Berlin, while Volkswagen and Audi have partnered with recycling specialists such as Umicore in Europe and Redwood Materials in Europe and the United States. Redwood Materials, a start-up created recently by a Tesla co-founder, already valued at billions of euros, has also closed agreements with BMW and Toyota, and Stellantis wants to follow in its steps with Orano. All these operations are, in part, a response to the spectacular power of Chinese electric car brands such as BYD, Cheri and SAIC, and Chinese battery recycling companies such as Ganfeng Lithium.
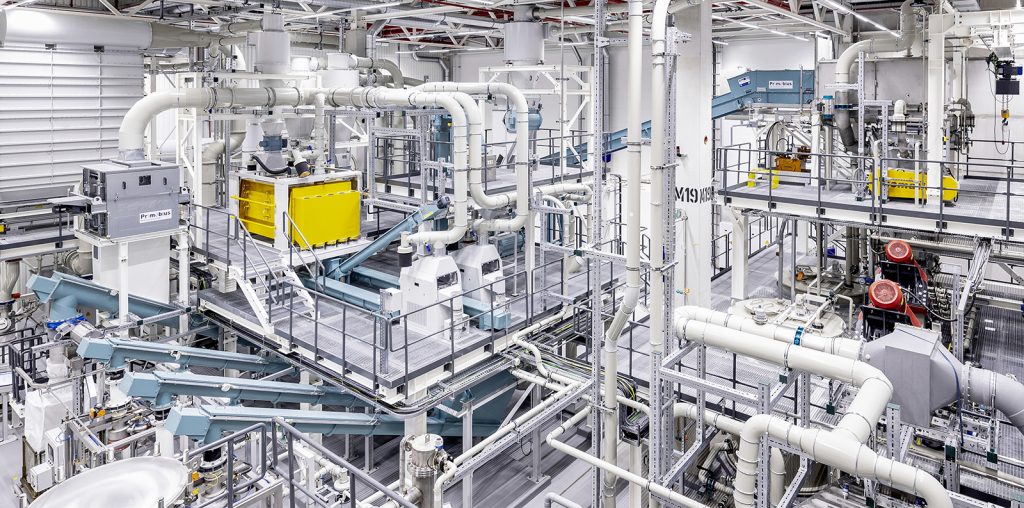
According to the International Energy Agency, around 80% of battery recycling is carried out globally in China, while Europe and the United States each represent less than 5% of the market. And everything seems to indicate that the West is being too slow to react: in the next five years, the agency does not expect the United States and Europe to each account for more than 10% and for China to control less than 70%.
In 2023, 50% of these factories would be devoted to process scrap from both defective and completely unrecoverable batteries. And the Mercedes-Benz plant in Baden-Baden is a good example.
According to the German giant, its plant classifies and separates plastics, copper, aluminum and iron in several stages. Thus, while the hydrometallurgical process deals with the active materials that make up the electrodes of battery cells (collectively known as black matter), cobalt, nickel and lithium are mined individually and can be used in the production of new cells. This process generates less waste than others (such as pyrometallurgical methods) and requires lower temperatures, thus consuming less energy. However, there are more options than those at the Mercedes-Benz factory. A prominent example: plants that reuse worn-out batteries taken from vehicles that are no longer useful because they have lost, through sheer degradation, more than half of their energy storage capacity.
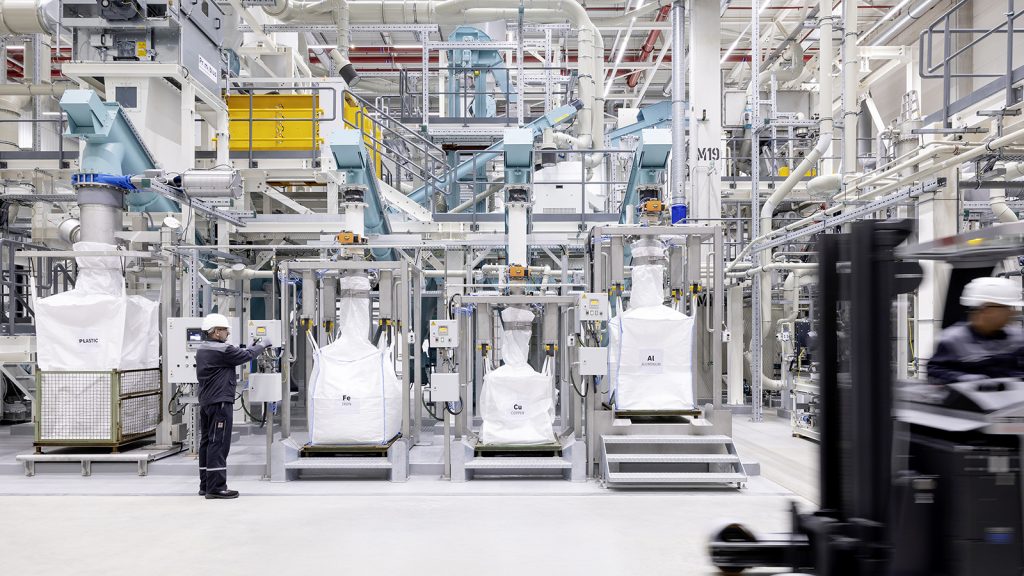
According to an analysis by S&P Global Mobility, China had around 20,000 electric battery recycling companies last year. And, although most are currently dealing with scrap recovery, it is expected that those that process severely degraded batteries for reuse outside of vehicles outperform them in terms of production in China in 2026.
We are referring to electric vehicle (EV) batteries whose capacity has degraded by between 60% and 80%, making them unsuitable for continued use in cars, but perfectly usable as stationary storage modules for the general electricity grid.
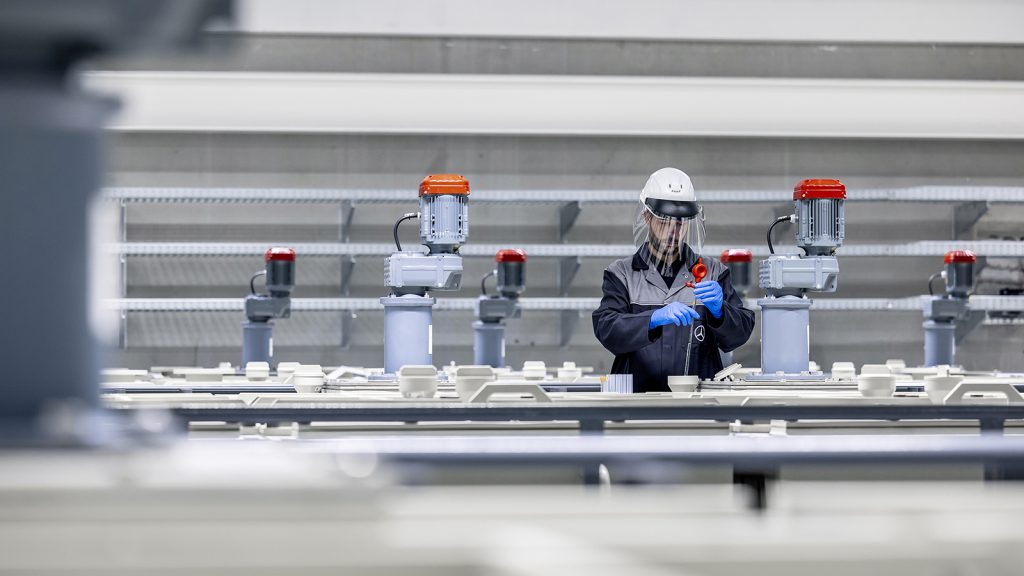
The next innovation
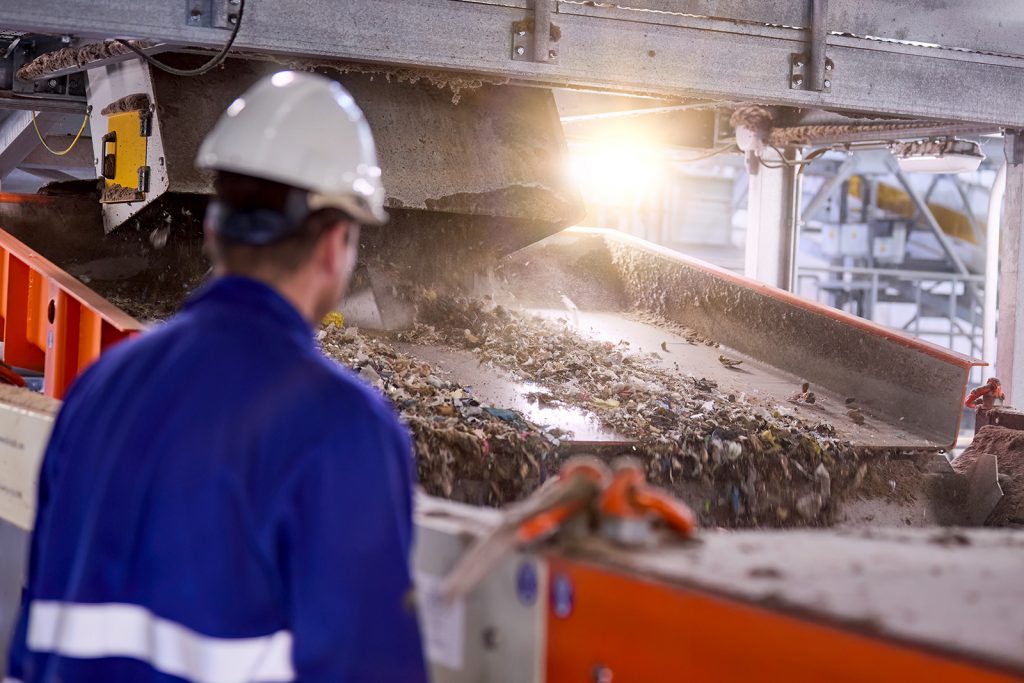
Another possibility for reusing batteries could be to start using, for short-term storage, those of EVs that are inactive (which is most of the time, in the case of private cars), but connected to the general electricity network. The technical feasibility of this process has been proven in over 100 pilot projects.
Both the batteries that would remain in the vehicles and those that are removed after a significant degradation could provide more storage to the network with less expenditure on materials than the production and installation of new batteries.
More specifically, according to a study by a team from the University of Norway published in Nature magazine in May, the sum, first, of using around 50% of EVs as storage units connected to the electrical grid while they are idle, and second, of offering 40% of significantly degraded batteries a second life, could completely cover the European Union’s need for stationary electricity storage by 2040.
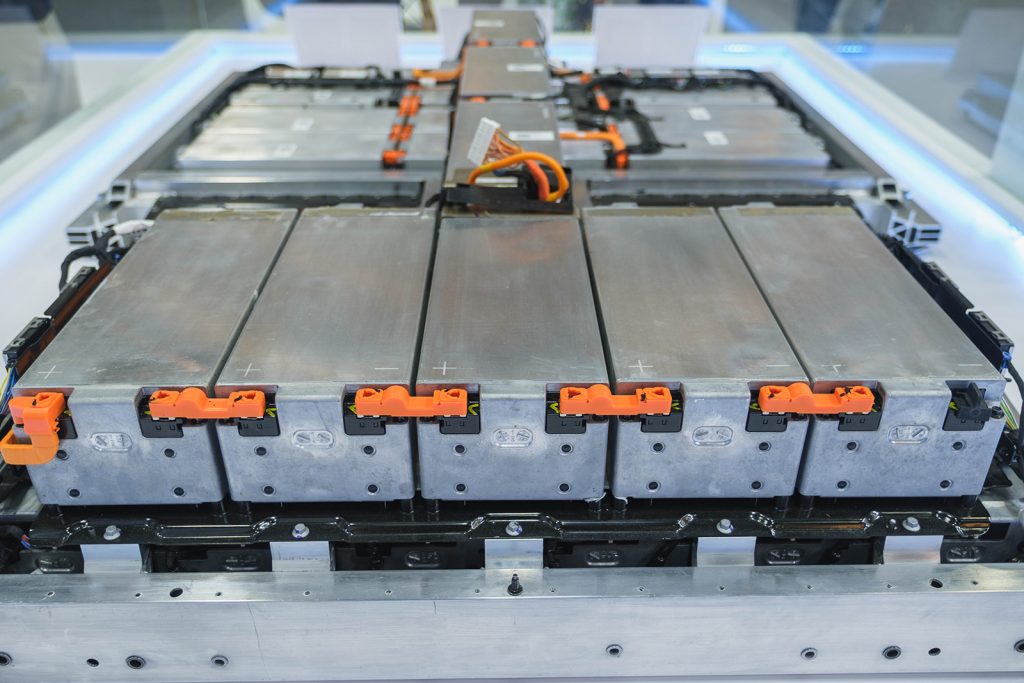
All of this, the study continues, “could reduce the total European demand for raw materials” between 2020 and 2050 by up to 7.5% and 1.5%, respectively, which could alleviate geopolitical risks and increase the energy and material security of the EU”. Additionally, “any excess capacity could be used as a strategic reserve to increase resilience to emergencies such as blackouts or adverse geopolitical events.”
Within ten years, according to an analysis by S&P Global Mobility, the giants of the automotive industry will have to manage the batteries of some 12 million EVs, which will have degraded enough through use to have to be converted into scrap metal, or be given a second life. They are the equivalent of 900 GWh in cobalt, nickel, lithium and manganese, four of the minerals used to make car batteries for electric vehicles.
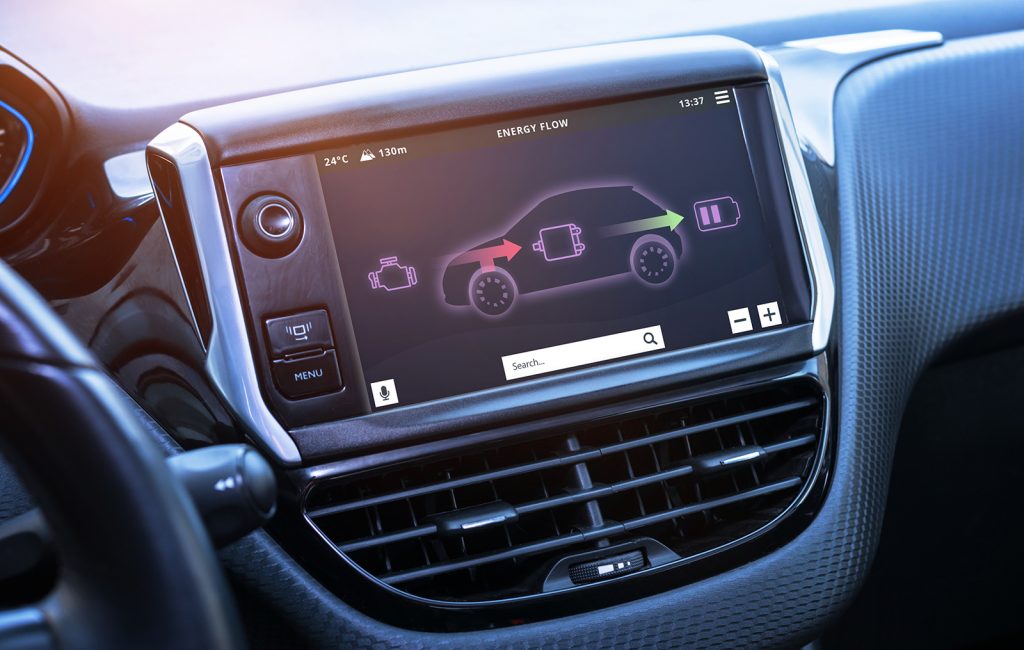
According to statistics from World Mining Data, the unstable Republic of the Congo controls about 70% of the world’s cobalt production, and a similar thing happens with manganese in South Africa and Gabon. On the other hand, China refines more than 60% of the cobalt and lithium produced globally, and Beijing can easily interfere in the international supply of these and other critical minerals for EV batteries, according to a recent study from Carnegie Mellon University.
And the “adverse geopolitical events” that complicate access to key raw materials are by no means a remote possibility in countries like Congo, South Africa and Gabon. The same can be said of a world where the United States has essentially closed its market to Chinese electric vehicles this year by raising its tariffs up to 100%, while the European Union, anticipating an influx, raised tariffs to 45% in October.
The multi-million dollar race to deploy the most efficient recycling initiatives for electric vehicle batteries is nearing boiling point between the world’s largest automotive giants. And that’s just the beginning, given that nobody knows for sure what the cars and the structure, capacity and composition of their batteries will be like in just a decade. The race is on.
Write: Gonzalo Toca