Countertops that become roads: new sustainability on asphalt
Over time, dirt roads were replaced with asphalt. Thanks to this change, accompanied by innovation in means of transport, distances were shortened. Movement became faster, but it led to the spread of a surface made from a mixture of petroleum derivatives. This type of material comes from non-renewable fuels and its processing has repercussions on environmental health, a worrying issue in times of climate crisis.
This is also changing. There are already initiatives that promote the manufacture of more sustainable roads. As in other sectors, concern for the environment calls for decarbonization. These techniques include using recycled plastic or an even more novel one: using waste from quarries to turn it into tracks. This is what Cosentino’s latest project consists of, which has just been put to the test in Andalusia.
According to the company, which specializes in manufacturing surfaces for architectural projects, new roads on the national map will emerge from these deposits where the history of humanity is pumped out. This will be obtained from the waste generated in the manufacturing process of Silestone countertops and Dekton surfaces.
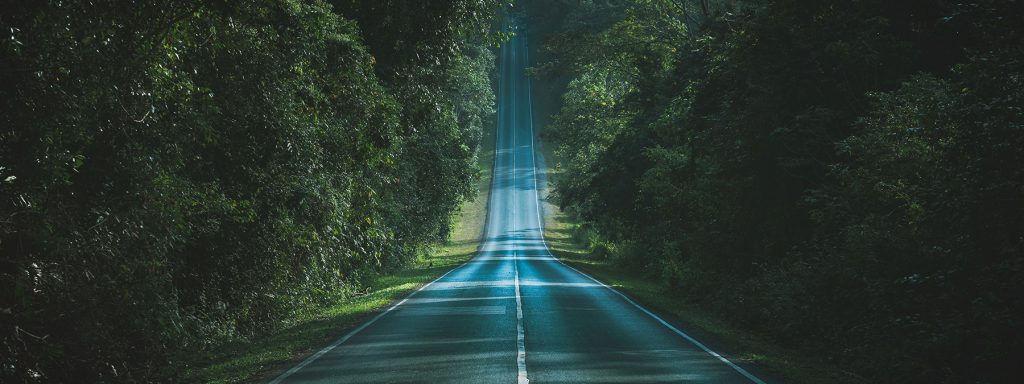
“Vamos a llevar a su máximo potencial el concepto de circularidad”, afirmaba Valentín Tijeras, director de innovación de Cosentino, al diario Abc. Esta iniciativa, detallaban, está respaldada por el Innovation Fund de la Comisión Europea y supone un desembolso global de 80 millones de euros. Eso la convierte en una de las “inversiones estratégicas” de la compañía en los próximos años. Su objetivo, alcanz“We are going to take the concept of circularity to its maximum potential,” said Valentín Tijeras, director of innovation at Cosentino, to the newspaper Abc. This initiative, they explained, is backed by the Innovation Fund of the European Commission and involves a global outlay of €80 million. This makes it one of the company’s “strategic investments” in the coming years. Its objective is to achieve zero waste.
First of all, it is important to explain what the term Silestone means. It is a surface made from different minerals and resins, widely used indoors, where the amount of silica has been reduced and recycled materials have been used. “In the calibration and polishing process, to ensure perfect planimetry, a few millimeters of thickness are subtracted, which in millions of slabs per year generates 200,000 tons of waste in the form of sludge,” said Tijeras regarding its new use. According to him, this material is filtered, but has a color and characteristics that prevent its subsequent reuse without a prior calcination and purification process, with a high energy cost.
Under the name CT Quarry, the goal of the project is to develop a pioneering industrial plant that integrates the use of renewable fuels and electric energy (while recovering heat from the process) to sustainably revalue more than 100,000 tons of this industrial sludge per year. “We will use part of it ourselves and the other part will go to other companies that can also use this material,” Tijeras pointed out. “With this, we create an ecosystem to revalue a resource that will no longer have to be stored in a landfill.”
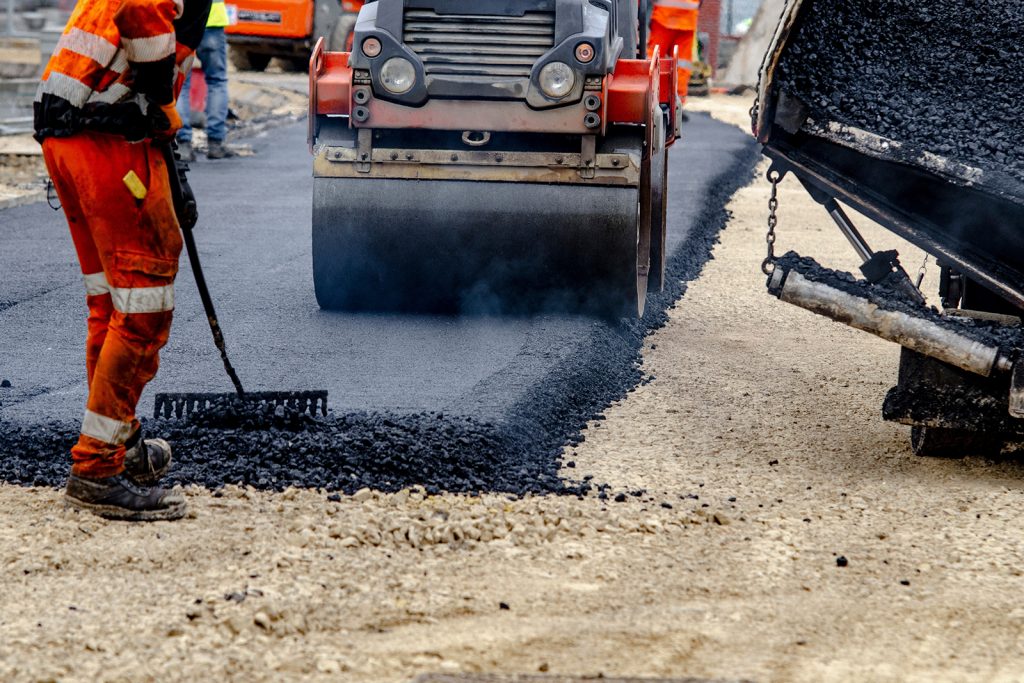
Cosentino hopes to fully revalue these tons left over from the Silestone manufacturing process. A fact that is preceded by other successful attempts. The company has already tested its HibriQ technology, which uses recycled products and reduces the use of quartz in Silestone by 40%. “With CT Quarry, the level of circularity increases and the use of silica is reduced, thus increasing the safety of the product,” said the director of innovation at Cosentino, highlighting that in the industrial complex in the Almería town of Cantoria is set one of the largest solar self-consumption solar parks in Spain (where it recirculates more than 90% of the water used in its processes).

“By producing alternative raw materials, the project advances the resilience of the European Union, its autonomy and energy independence,” Tijeras stressed, referring to the fact that European aid is subject to the achievement of certain objectives, such as the reduction of polluting emissions by more than 60%. CT Quarry will also give a second life to other company waste. For example, to the ‘tejos’, those cuts made in Silestone boards when they are adapted to the space they occupy in a house.
The project also includes a solution to the waste generated in the manufacture of Dekton, a surface that is manufactured using high-pressure and high-temperature processes. Currently, this type of waste is stored “in an orderly manner” in a large quarry, within the perimeter of the Cantoria industrial center. With this project, which is run from a building with 11 laboratories and 130 professionals, it will be converted into useful material.
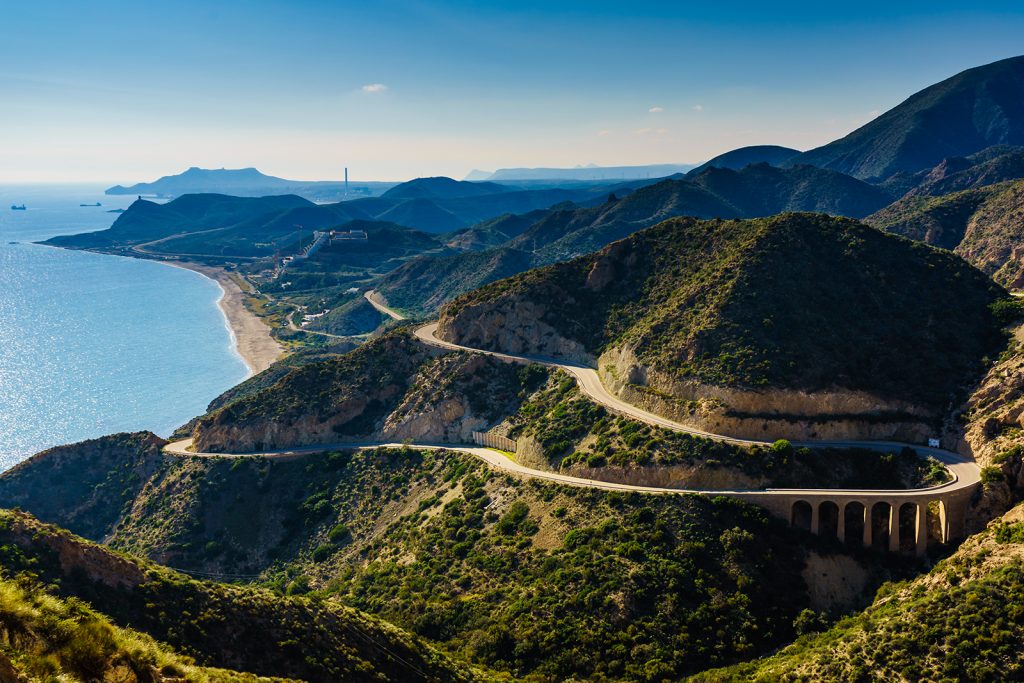
“We promote a scalable model that can contribute to decarbonization in resource-intensive industries, from glass to ceramics and other construction materials,” said Tijeras, adding that CT Quarry proves that “all waste is a potential raw material for future development.”
And they will test it on a road in their province, Almería. The Junta de Andalucía has already announced the agreement to use it along a 600-metre stretch of the A-1204 road, in Albox. Rocío Díaz, the regional minister for development of the Autonomous Community, defended this type of sustainable tarmac and advocated “innovation and research” in asphalts that “not only serve to improve our roads, but are also more respectful of the environment.” “The residual sludge generated by Cosentino becomes an opportunity and a resource for our asphalt mixtures”, stressed the official, taking a further step in this paradigm shift when it comes to travelling.