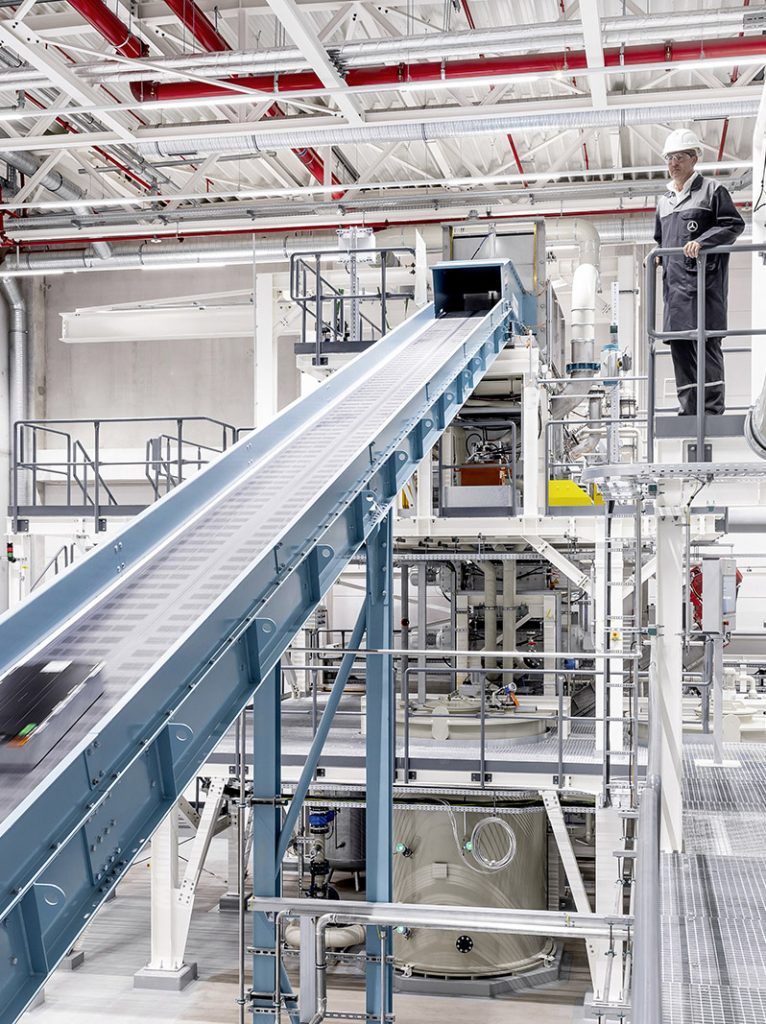
Mercedes-Benz abrió, a finales de octubre, una planta en Baden-Baden para reciclar unas baterías de las que espera recuperar más del 90% de sus materiales. La competición tan solo acaba de comenzar.
El gigante alemán asegura que su nueva factoría tiene una capacidad productiva anual de 2.500 toneladas y que los materiales recuperados alimentarán la producción de más de 50.000 módulos de baterías para sus nuevos coches totalmente eléctricos.
Un análisis de S&P Global Mobility espera que, en 2032, los minerales recuperados de las pilas usadas equivalgan al 21% de la demanda mundial de cobalto y al 19% de la demanda total de níquel. Y los gigantes europeos y estadounidenses de la automoción han empezado a reaccionar, más, si cabe, después de que disparasen su adquisición de baterías el año pasado hasta darse de bruces con una crisis de abastecimiento.
Y aquí no solo hablamos de Mercedes-Benz. Tesla está adosando plantas parecidas a la de Baden-Baden en sus Gigafactories de Texas y Berlín, mientras Volkswagen y Audi se han asociado con especialistas en reciclaje como Umicore en Europa o Redwood Materials en Europa y Estados Unidos. Redwood Materials, una start-up creada recientemente por un cofundador de Tesla y valorada ya en miles de millones de euros, también ha cerrado acuerdos con BMW o Toyota, y Stellantis quiere seguir sus pasos con Orano.
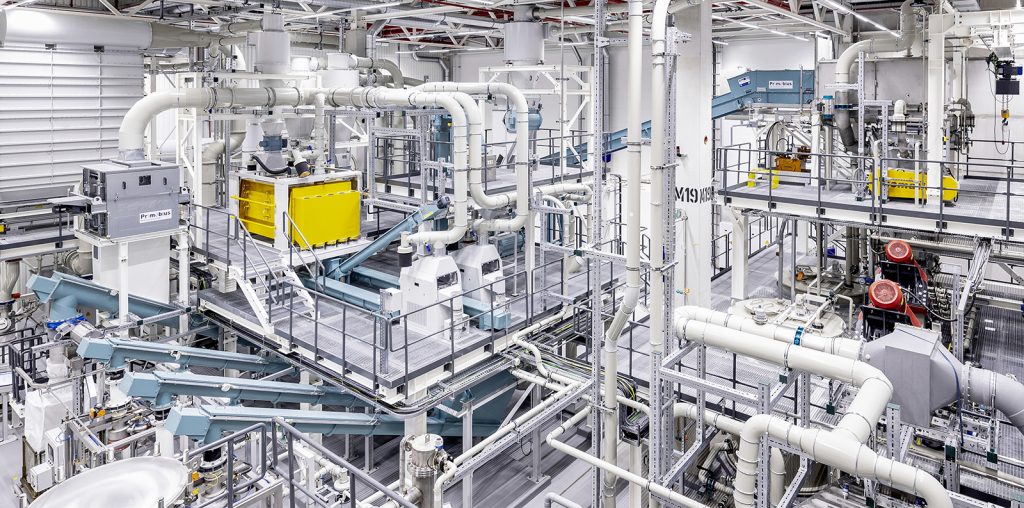
Todas estas operaciones son, en parte, una respuesta al espectacular poder de marcas chinas de automoción eléctrica como BYD, Cheri o SAIC y de proveedores chinos de reciclaje de baterías como Ganfeng Lithium.
Según la Agencia Internacional de la Energía, alrededor del 80% del reciclaje de baterías se lleva a cabo mundialmente en China, mientras que Europa y Estados Unidos representan menos de un 5% del mercado cada uno. Y todo parece indicar que Occidente está tardando en reaccionar: en los próximos cinco años, la agencia no espera que Estados Unidos y Europa concentren cada uno más del 10% y que China controle menos del 70%.
En 2030, estas factorías se dedicarían mundialmente, en un 50% de los casos, a procesar la chatarra de las pilas tanto defectuosas como completamente irrecuperables. Y la de Mercedes-Benz en Baden-Baden es un buen ejemplo.
Según el gigante alemán, su planta clasifica y separa plásticos, cobre, aluminio y hierro en varias etapas. Así, mientras el proceso hidrometalúrgico se ocupa de los materiales activos que componen los electrodos de las celdas de la batería (conocidos, en conjunto, como masa negra), el cobalto, el níquel y el litio se extraen individualmente y pueden utilizarse en la producción de nuevas celdas. Este proceso genera menos residuos que otros (como el pirometalúrgico) y necesita temperaturas menos elevadas, por lo que consume menos energía.
Sin embargo, hay más opciones que las de la factoría de Mercedes-Benz. Un ejemplo prominente: las plantas que reutilizan baterías desgastadas por el uso y extraídas de unos vehículos a los que ya no les sirven porque han perdido, por pura degradación, más de la mitad de su capacidad de almacenamiento de energía.
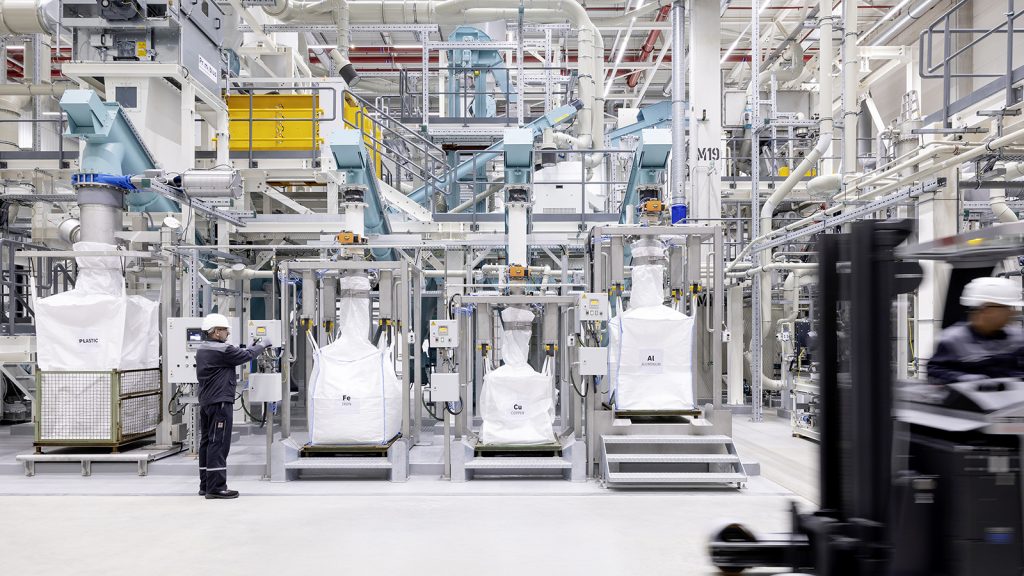
Según un análisis de S&P Global Mobility, China poseía alrededor de 20.000 empresas de reciclaje de baterías eléctricas el año pasado. Y, aunque la mayoría se ocupen actualmente de la recuperación de la chatarra, se prevé que las que procesan pilas fuertemente degradadas para reutilizarlas fuera de los vehículos las superen en producción en China en 2026.
Hablamos de baterías de vehículos eléctricos (EV, por sus populares siglas en inglés) cuya capacidad se ha degradado entre el 60% y el 80%, lo que las hace inadecuadas para su uso continuado en los coches, pero perfectamente aprovechables como almacenamiento estacionario para la red eléctrica general.
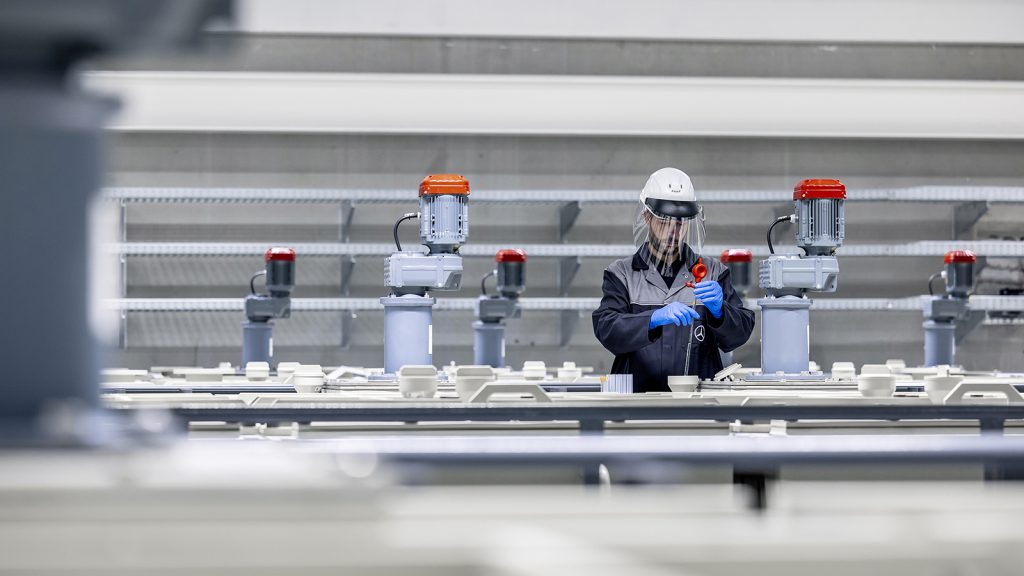
La próxima innovación
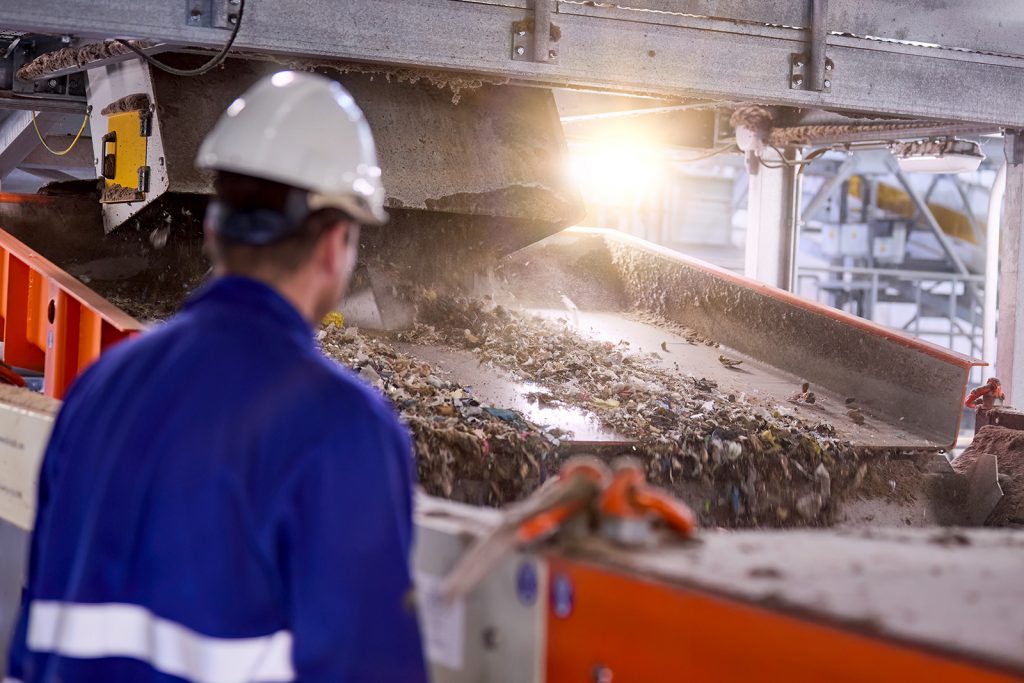
Otra posibilidad de reutilización de baterías podría pasar por empezar a aprovechar, para el almacenamiento a corto plazo, las de los EV que están inactivos (la mayor parte del tiempo, en el caso de los coches particulares), pero conectados a la red general de suministro eléctrico. La viabilidad técnica de este proceso se ha demostrado en más de 100 proyectos piloto.
Tanto las pilas que seguirían en los vehículos como las que se retiran tras una fuerte degradación de su capacidad podrían proporcionar más almacenamiento a la red con menos gasto en materiales que la producción e instalación de baterías nuevas.
Más concretamente, según el estudio de un equipo de la Universidad de Noruega publicado por la revista Nature en mayo, la suma, primero, de utilizar alrededor del 50% de los EV como unidades de almacenamiento conectadas a la red eléctrica mientras están inactivos y, segundo, ofrecerles al 40% de las baterías fuertemente degradadas una segunda vida, podría cubrir completamente la necesidad de la Unión Europea de almacenamiento eléctrico estacionario para 2040.
Todo ello, sigue el estudio, “podría reducir la demanda total europea de materias primas entre 2020 y 2050 hasta en un 7,5% y un 1,5%, respectivamente, lo que podría aliviar los riesgos geopolíticos y aumentar la seguridad energética y material de la UE”. Además, matiza, “cualquier capacidad excedente podría utilizarse como reserva estratégica para aumentar la resiliencia frente a emergencias como apagones o eventos geopolíticos adversos”.
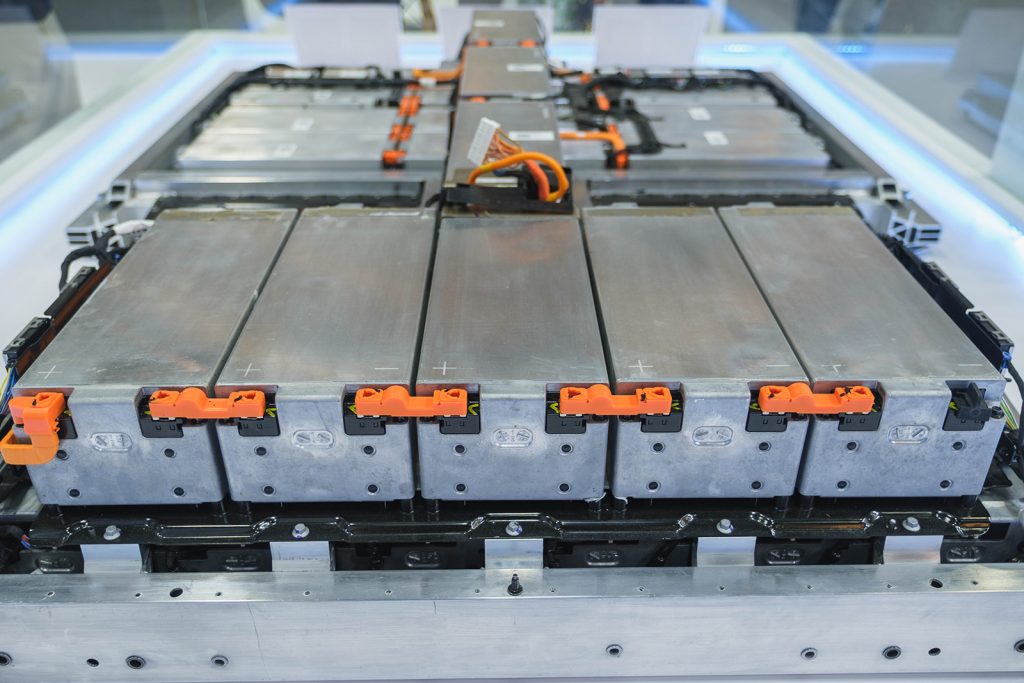
Antes de diez años, según un análisis de S&P Global Mobility, los gigantes de la automoción deberán administrar las baterías de unos 12 millones de EV, que se habrán degradado lo suficiente por el uso como para tener que convertirlas en chatarra o darles una segunda vida. Son el equivalente a 900 GWh en pilas de cobalto, níquel, litio o manganeso, cuatro de los minerales con los que se fabrican las baterías de los vehículos eléctricos.
Según las estadísticas de World Mining Data, la inestable República del Congo controla alrededor del 70% de la producción mundial de cobalto, y ocurre algo parecido con el manganeso en Sudáfrica o Gabón. Por otra parte, en China se refina globalmente más del 60% del cobalto y el litio y Pekín puede interferir fácilmente en el suministro internacional de estos y otros minerales críticos para las pilas de los EV, según un estudio reciente de la Universidad Carnegie Mellon.
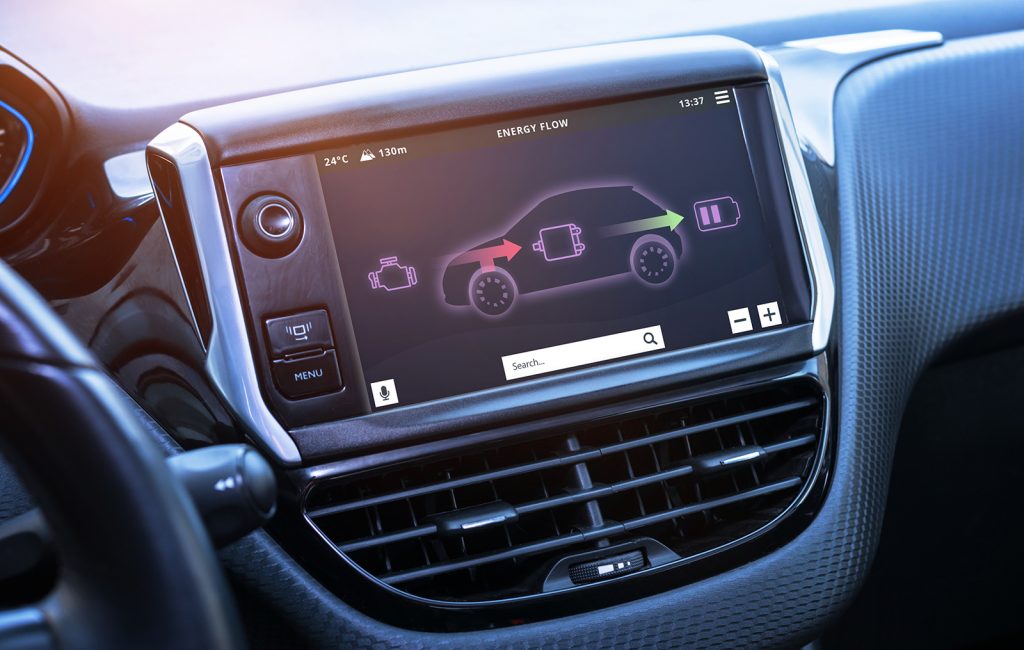
Y los “eventos geopolíticos adversos” que compliquen el acceso a materias primas críticas no son ni mucho menos una posibilidad remota en países como Congo, Sudáfrica o Gabón. Lo mismo puede decirse de un mundo donde Estados Unidos ha cerrado este año de facto su mercado a los vehículos eléctricos chinos subiendo sus aranceles hasta el 100%, y la Unión Europea, previendo una llegada torrencial, ha elevado los suyos hasta un 45% en octubre.
La carrera millonaria por desplegar las iniciativas de reciclaje más eficientes para las baterías de vehículos eléctricos se está aproximando a su punto de ebullición entre los mayores gigantes mundiales de la automoción. Y eso que solo acaba de comenzar y que nadie sabe con certeza a qué se parecerán los coches y la estructura, composición y capacidad de las baterías de los vehículos eléctricos dentro de tan solo una década. El pistoletazo de salida acaba de sonar.
Escribe: Gonzalo Toca